Millions of bricks are manufactured every year all over the world. But have you ever stopped to wonder how they get made?
Brickmaking has changed significantly since we first started making them. The process has, of course, been refined over the years and now modern brick manufacturing follows a very particular process.
In this post, we'll be going through how a typical kiln-fired brick is made - and if you're looking to buy some bricks for an upcoming project, our team is standing by to help you get what you need at the best prices.
Request a quoteThe raw materials
The main ingredient of most bricks is clay. It always has been. There are certain clay minerals that are more suited to making bricks and often the location of the clay can have an impact on the colour of the end product.
Another big component is sand and some bricks also contain other additives such as lime, iron oxide and magnesia which offer other benefits. The final crucial ingredient in the brick making process is water.
There are certain minerals that are more suited to making bricks and they can have an impact on the colour of the end product
Making it work
What about the manufacturing process itself. Not every brick you see will be made in the format we explain below, but many fired bricks are.
1 Crushing/grinding
First off, the dry, raw clay material is crushed and ground in what's called a jaw crusher. This turns the material into smaller particles and it's at this stage that the other materials are added. Different size pieces are separated, and larger pieces are set aside for pummelling so they can be used in another batch.
2 Forming
There are several options for this stage. Extrusion (or wire cutting) is the most common because it's the lowest cost method for producing bricks at scale - it's very much the mass-produced option.
Extrusion
After crushing, the pulverised material is fed into one end of a pug mill. The material is then folded together so it's all properly mixed. It's then fed into the extruder where it goes through a further two phases - all the air is removed in a vacuum and the material is compacted.
The brick shape is formed by pushing the material through a die. This is an orifice in the end of the machine shaped into the cross section of a brick. Sections of the desired length are then cut off with saws or wires or in some cases a long cable is formed and then cut into segments from there.
The dies allow for a certain degree of versatility in production. For example, cylindrical sections can be included to create holes in the brick.
Moulding
Soft wet clay is shaped by a mould. With handmade bricks this clay will be thrown into the mould - often a wooden box coated with sand and left to dry.
In larger-scale manufacturing, a hydraulic press will compact the material into the required shape. The sand on the inside of the mould helps with the removal of the brick and gives it a certain surface texture.
Pressing
This is similar to the moulded method, but it uses much thicker clay and greater force in pressing. The thick clay mix has a lower water content which when pressed leads to a more accurate, sharper-edged brick. The material is placed in a die and then compacted with a steel plunger. This can be set at different pressures.
These plungers often feature 'frogs' - the indent you see in the top of some bricks - and will have that sharper outline. This is a more expensive process, particularly as longer firing is usually required, but it creates much more durable bricks.
3 Extra steps
Depending on the requirements of the bricks, some manufacturers may choose to include some additional steps. These include chamfering, which involves having a roller to make an indent or apply a furrow as it exits the extruder.
Some bricks may also be coated with sand, either by a vibrating machine coater, pressure roller or for the hardest material, a sand blaster.
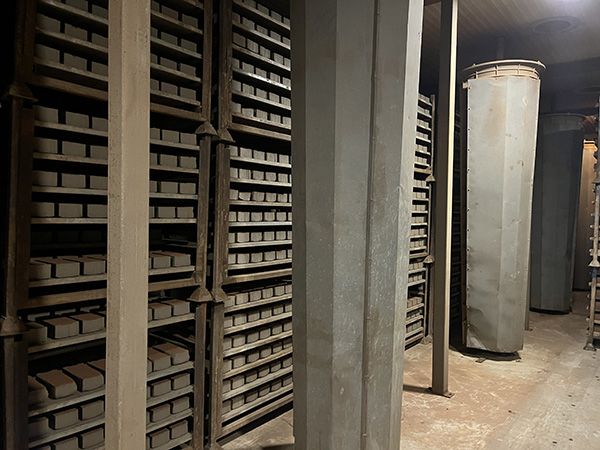
4 Drying
Once the brick itself has been made, it needs to dry. Removal of excess moisture is important. If it's not removed, it will evaporate too quickly during firing and cause cracking, thus ruining the brick.
There are a couple of ways to dry large amounts of brick. For a long time, the most common way of doing this was by using tunnel dryers.
These consist of a long chamber through which the fresh ware is slowly pushed. Fan circulated hot air is forced into the dryer covering the bricks. Automatic chamber dryers are also in wide use. Bricks sit on extruded bars and are placed in rows where they are dried in the heavily regulated climate.
5 Firing
The next major step in making bricks is the firing process. Generally, bricks will stay on the same cars used for the drying process to take them into the kiln. This is where firing takes place.
Kilns have evolved significantly over the years, increasing capacity, consistency and economic efficiency. Most kilns in operation are tunnel kilns, whereby bricks are pushed through a long, specially built tunnel, whilst being fired.
They used to be high and narrow. Now they're generally lower and wider, allowing more bricks to be fired at once. Most bricks these days are gas fired in order to better regulate a continuous temperature. But in some cases, a coal fire may be used.
6 Unloading
The final part of the process involves allowing the bricks to cool and then be unloaded. They are removed or 'de-hacked' from the cars and then 'set' in stacks where they can then be wrapped and packaged for distribution.
We're here for you
If you hadn't realised, we love bricks. And we love finding out where they come from.
If you're thinking about starting a building project, we have a range of services tailored to help you achieve successful brickwork - whatever the shape of your build or the size of your ambition.
Our expert Brick Advisors are standing by to help you match, customise and calculate the exact amount of bricks you need, then source them and find the best price - we'll even arrange delivery too.
Simply let us know what you need, and our experts will do the rest!